Sistem ERP in FMCG: SFA, portal WEB, planificare livrari, picking, WMS
Sistemul ERP si planificarea livrarilor
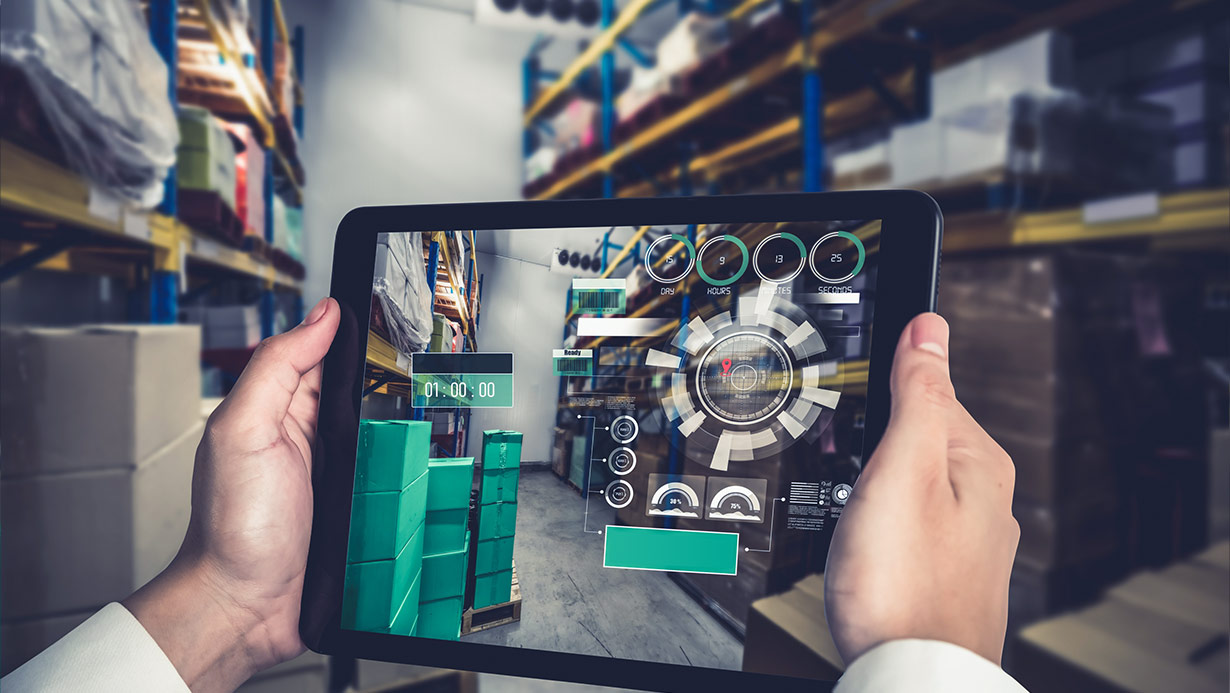
Preluarea comenzilor poate fi automatizata in mare masura prin implementarea SFA (Sales Force Automation) pentru agentii de vanzari sau a unui portal WEB de preluare a comenzilor (Business to Business sau Business to Consumer). Pentru a fi receptionate rapid comenzile emise prin intermediul dispozitivelor mobile, este recomandat ca acestea sa lucreze in mod conectat permanent. Din fericire, costurile de comunicatie sunt in continua scadere, calitatea serviciilor oferite si gradul de acoperire avand un trend crescator.
Pe langa avantajele legate de logistica livrarilor, implementarea celor doua solutii informatice au multiple alte avantaje: reducerea considerabila a pierderilor datorate rotatiei personalului, controlul asupra calitatii procesului de vanzare, cresterea gradului de acoperire a pietei etc.
Indiferent de canalul de vanzari, comenzile odata introduse in sistem si validate, urmeaza un workflow de natura logistica. Acesta are cateva etape distincte: planificarea livrarilor, pickingul, incarcarea marfii in masini si livrarea efectiva.
Planificarea livrarilor
De obicei o firma de distributie de peste un anumit nivel are activitatea distribuita in mai multe puncte de lucru pentru a putea acoperi zonele geografice in care ofera servicii. Clientii (sau punctele de lucru ale clientilor) sunt alocati punctelor proprii de lucru. In interiorul punctului de lucru, activitatea operationala este impartita pe zone operationale (zone de vanzare specifice agentiilor comerciale si zone de livrare specifice masinilor sau rutelor).
Fiecare zona de livrare are atasat un program de vizita, planificarea masinilor si soferilor pe ruta respectiva. Statistic, se poate determina o perioada medie necesara in vederea pregatirii unei comenzi pentru un anumit client / gama de clienti.
Avand aceste date, din momentul preluarii comenzii in sistem, se poate dermina cu precizie momentul livrarii, ruta de livrare, masina si soferul care vor efectua livrarea. Astfel, in functie de aceasta planificare comenzile vor fi trimise spre picking. In practica exista multe variatii pe aceasta tema: daca marfa nu exista in acest depozit, dar poate fi livrata din altul, daca marfa trebuie intai transferata din depozitele centrale, daca apar disfunctionalitati ale parcului logistic etc. Pentru astfel de probleme exista instrumente specifice capabile sa eficientizeze deciziile corective.
SeniorERP ofera doua tipuri de WMS:
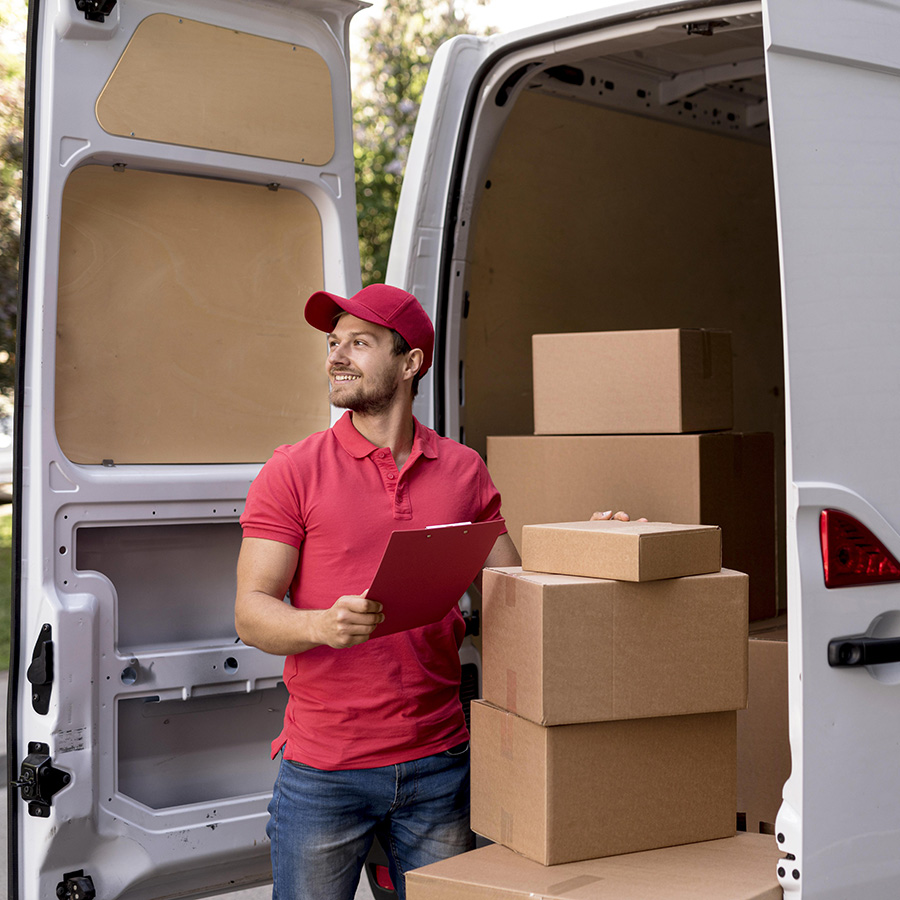
Pregatirea comenzilor Pickingul si livrarea efectiva
Odata finalizat picking-ul, marfa se transfera in zona de livrare. Daca s-a efectuat picking la nivel de zone, aici se recompun comenzile sau se grupeaza pe livratori. In masini, produsele vor fi incarcate in ordinea inversa descarcarii (daca pickingul a fost executat la nivel de comanda), sau in functie de experienta soferului (daca s-a incarcat cumulat), comanda urmand sa fie recompusa in momentul livrarii.
Din punct de vedere informatic, solutia la aceasta problema poarta denumirea de WMS – Warehouse Management System. Rolul acestui sistem este de a crea si controla fluxurile de lucru in depozit. Spre exemplu, se poate urmari in orice moment starea unei comenzi (Ex: Deschisa, In curs de picking, Picking finalizat, Verficata, Livrata partial, Livrata integral, Inchisa etc), se pot calcula indicatorii de performanta ai operatiunilor de picking, se poate cuantifica pierderea datorata situatiilor de out-of-stock, se pot automatiza operatiunile de lucru.